METAL STAMPING
PROJECT SERVICES
PROJECT SERVICES
Every project – no matter how small the piece or quantity – requires critical evaluation and engineering expertise. This stage of the project ultimately effects the quality of the product, the speed in which it can be manufactured, and the final end product cost. Each operation is closely scrutinized so that every project is completed in the most timely and economical fashion.
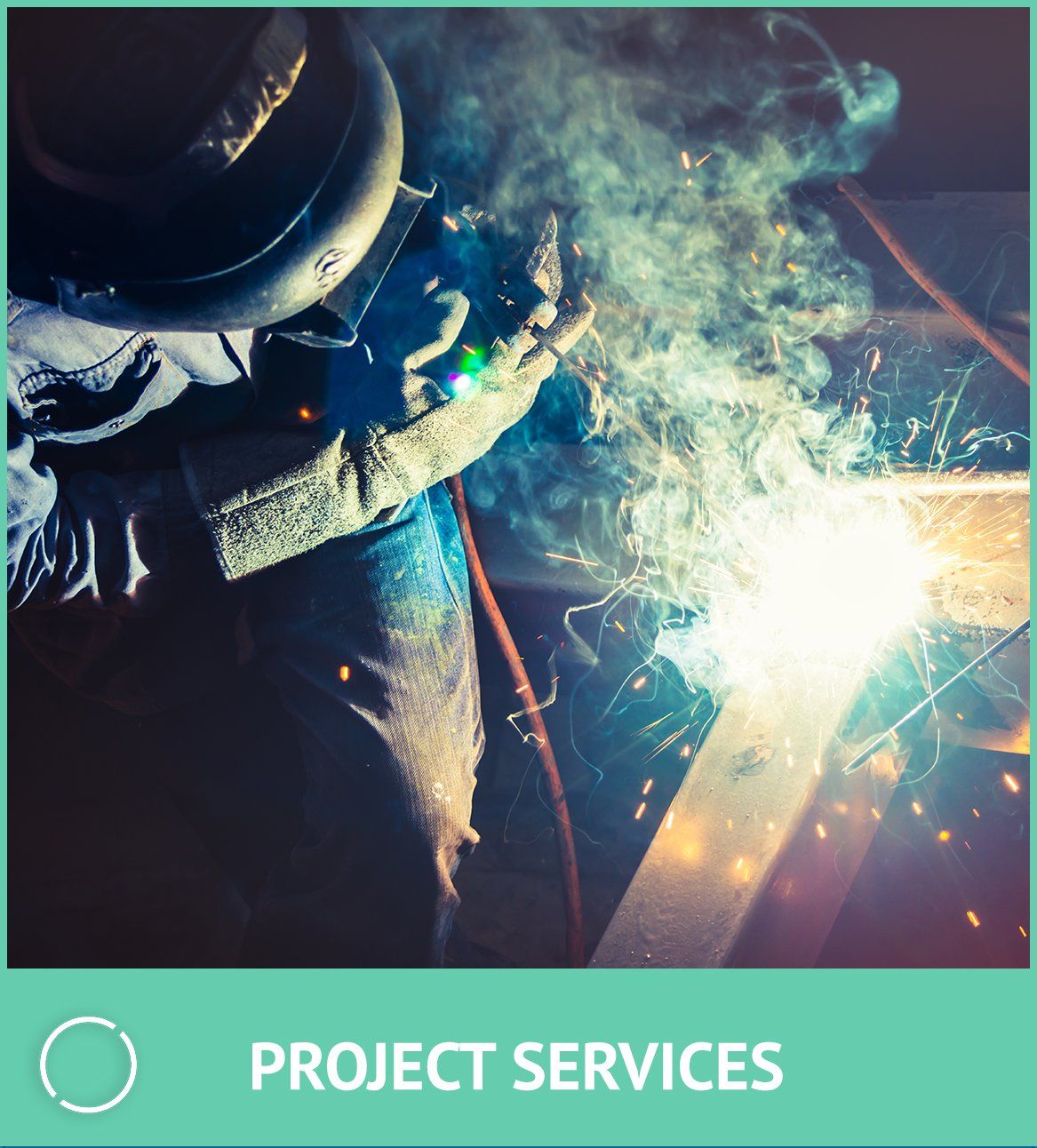
We feel every aspect of the project is an important service to our customers, therefore we own the process from start to finish.
1
WELL WILL TAKE THE PRINT
2
MAKE OUR OWN TOOLS
3
DEVELOP THE SHELLS
4
CONDUCT A FIRST ARTICLE INSPECTION
PPAP (if required)
Once the inspection process has been approved, we complete fitting up our presses and begin to run production knowing that our output is meeting the customer requirements.
In addition, we take care of all secondary services that may be required.
These services range from cleaning, deburring, threading, heat treating, plating, passivation, and some assembly.
COMMITMENT
Our customers have put their faith in us and we are committed to handle all aspects of their parts creation so they know they are in safe, reliable hands every time they come to us. This is the cornerstone of our business and our customers expect nothing less. Our stock room is provided to insure clean, dry and orderly storage of our raw materials enabling us to keep tight control of every large volume run, and assure that material costs are kept to a minimum.
METAL STAMPING CAPABILITIES
DEEP DRAWN
For our Deep Draw Stamping operations we exclusively run Waterbury Farrel presses ranging in all five standard sizes of 5, 10, 12, 15, & 20. These high-speed transfer presses allow for cost reduction, easy tooling change and shorter downtime for quick turnover. These qualities allow us to be competitive in deep draw components manufacturing. We can deep draw the following materials: Aluminum, Brass, Copper, Cold-Rolled Steel, Galvanized Steel, Stainless Steel, Tin-Coated Steel